At the beginning of this week I decided to go in a clamp up the two sides together ready for today's lesson. I also had to re-glue one of the stretchers as it hadn't glued correctly.
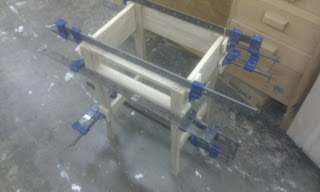 |
Above: Table glued together |
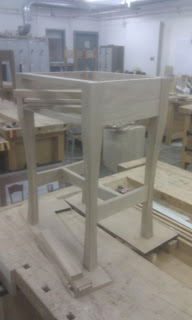 |
Above: Table un-clamped |
Today's lesson was hectic. I began by putting a face and edge on the three boards for the table top. However I hit a problem whilst putting a face on one of the boards which lead to it having to be at 17mm rather than 19mm.
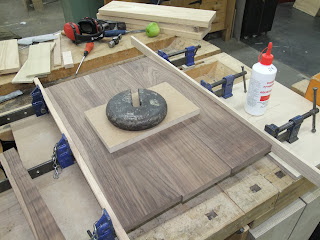 |
Above: Table top glueing up |
Whilst the top was gluing up I thicknessed and got the drawer front to fit the table.
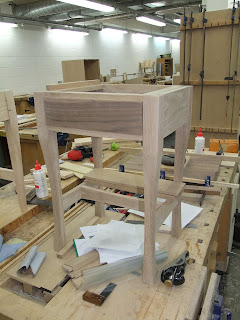 |
Above: Table with drawer |
After this I used the table router to make the grooves for the drawers. Originally I wanted to dovetail the drawer, however I couldn't find a dovetail jig in time, so decided to use these joints
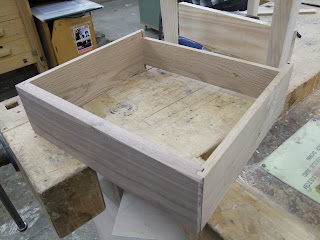 |
Part assembled drawer |
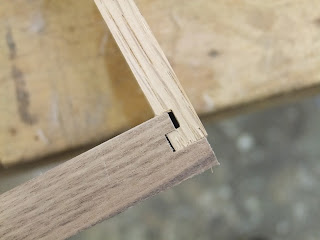 |
Above: Drawer joint being test fitted |
I also cut the MDF base and joined pieces of veneer to use which is the same as the rest of the table, however the veneer press heater is currently broken, so I had to leave it in until tomorrow to dry so I couldn't take any photos.
Finally just before I left I un-clamped the tabletop, and below is a picture. All I need to do now is sand it down and the use the overhead router to put my inlay in the top and drawer front.
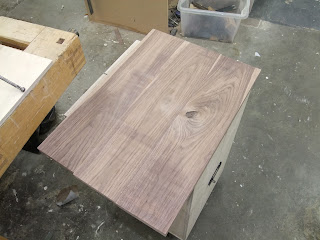 |
Above: Table top unclamped |