I spent the beginning of the day fitting the drawers and making a wooden base. Fitting the drawers was simple but time consuming, and the drawer base is used as the drawer stop. The base was made out of a piece of wood which was the same size as the base, and then cut with 2/3rds on one side, and one 3rd on the other. This meant that there is a base for one side to sit on whilst shut, and an equal base to fix wheels into place.
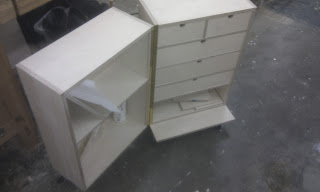 |
Above: Drawers fitted and base installed. |
I then decided to go buy some extras for the toolbox during lunch. This included wheels, a hasp, a lock and also another hinge. When I got back, the first thing was to fit the wheel. There are six wheels in total, four for the big base, and two for the small base. Two of these wheels are lockable, so you can stop it from moving.
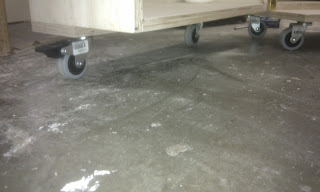 |
Above: Wheels fixed to the base of the toolbox |
After fitting the wheels, I then added the hasp and lock.
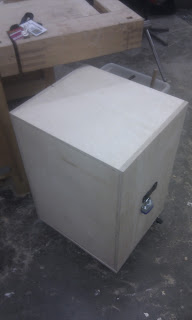 |
Above: Hasp and Lock |
After I completed these tasks, I decided to make my own modifications, as the wood for the table had not come in. The first thing was to fit a hinge and cut a door inside the cabinet. This is going to be used to hold my chisels in a rack that I made. I drilled a handle in the top left hand corner, similar to the drawer handles.
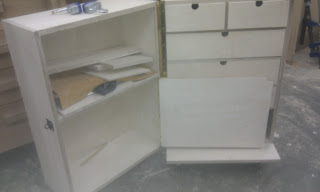 |
Above: Inside door hinged. |
I then began work on the chisel holder. I started by marking out and drilling holes the size of each chisel (as they were all slightly different). I also added two extra holes for any chisels I might get in the future. Then using the band saw I cut slots to each hole to slide the chisels in.
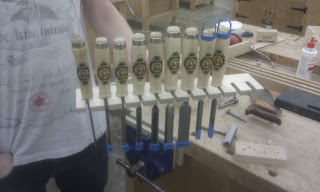 |
Above: Chisel holder with chisels. |
I originally planned to fix this to the back of the door, however I then thought it would be better if I could take the chisels all out at the same time and put them onto the bench. Therefore I made a free standing chisel holder.
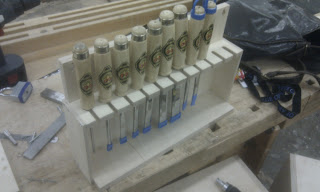 |
Above: Free standing chisel holder |
I then made two drop screw holes in the chisel holder, and put two screws into the back of the door. This allows me to hang the chisels securely, but also take them out whenever required.
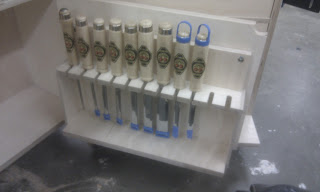 |
Above: Chisel rack fitted to door |
Finally I made two saw holders on the back of the cupboard, so they wouldn't get damaged in a drawer, and are easily accessible.
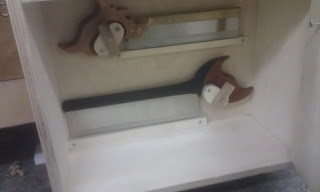 |
Above: Saw holders. |
Overall for this part of the module things went relatively smoothly, and allowed me to use the basic machines in the workshop. I am glad I had time to customise my own side of the toolbox which was not limited to the module requirements, as I will be using it for many years to come, and do not know if I would have time in the future.