This was the first lesson for Machine Production Techniques, and we began by having a module briefing.
In the module briefing we spoke about what was required for the toolbox and also about the table with a drawer. After we received a booklet with information about the module, we learnt about how to set up and use a router.
The first thing was how to put a cutting piece into the router. To begin with you first lock the cutter into place using the press button, and then using a spanner undo the bolt.
Once the bolt is done, you can then put the cutter piece into the router. You simply slide it inside the bolt. One important thing is to make sure you go to at least the flat line pictured on the cutter, so you can not see the arrow head. Finally you just had to re-tighten the bolt to thumb pressure.
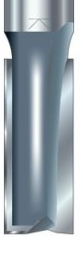 |
Minimum cutter depth |
Once this was in place, we then learnt how to start the router. This is simply done by the right hand. To start you have to push the safety switch down with your thumb, and then pull in the finger trigger towards you. You can also lock the router on so it stays on at all time, and this is done by applying some more pressure to the thumb trigger and then realising it.
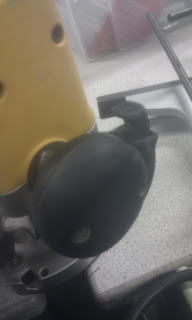 |
Right handle with thumb and finger trigger. |
I then learnt another important thing when using a router, and that is the direction of cut. This means that when you are creating a rebate you want to be pushing it into the material, to stop it from catching the material and tearing the material. This can cause the router to jump towards you, and be very dangerous. The direction is clearing shown on the base of the router.
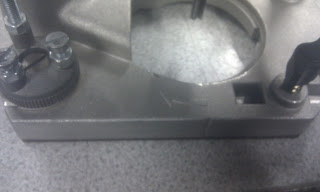 |
Direction of cut shown on the base of the router |
I then learnt the way to set the router for certain cuts, and this includes the depth of the cut. TO plunge the router into a material, you first realise the left handle by twisting it, and this then freely moves the router up and down. You then twist the handle again to lock it into place.
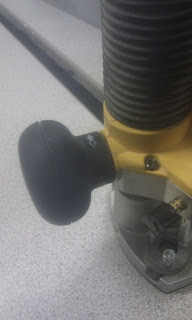 |
Arrows showing twisting motion of handle |
You can also set the depth using a depth stop, this is done by realising a wing nut on the side, and then twisting the bar to the bottom, this can be re-zeroed depending on different cuts.
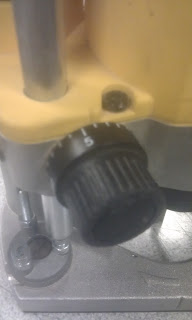 |
adjusting screw |
You can also place the object that your rebating underneath the bar, so you easily cut to the right height.
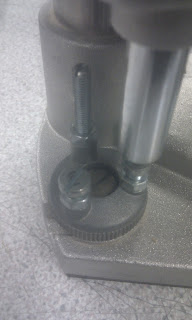 |
Area where you can place certain objects |
Finally I learnt about the fence that you put on the router, and this allows you to make parallel cuts at any distance from the edge of the piece of wood.
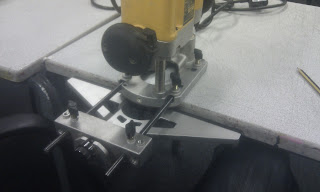 |
Router with fence attached |
The first day was interesting as we learnt about the module, and also how to correctly set up a router, the hardest part was to learn how to lock the router so it would carry on when you realised the trigger.