Over the last week and today's lesson I have managed to get of the other joints complete, but the main focus of this lesson was veneering. I will be veneering both the back panel, and also the drawer bottoms.
I first learnt about different types of veneering:
The first kind of veneer is called 'Running Veneer', which is when two pieces of veneer are joined together, with the grain going in the same direction on both piece.
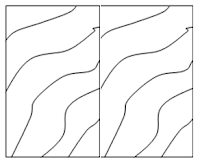 |
Running Veneer
The next is called 'Book Matched'. This is when two pieces of veneer are joined together, with the grain going in the opposite directions, and look like the pages in a book.
|
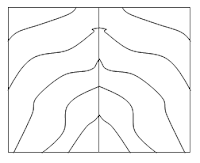 |
Book Matched Veneer |
Thirdly this pattern of veneer is 'Diamond'. Diamond is when four pieces of veneer are joined together, and the grain flows smaller into the center, creating a diamond shape.
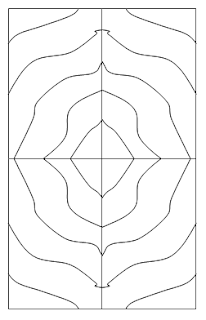 |
Diamond Veneer |
The last pattern is the 'Reversed Diamond', which is the same as the previous pattern, but the grain flowing in the opposite direction.
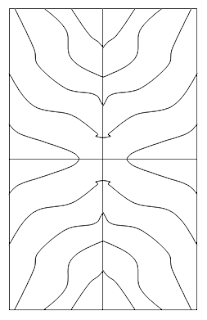 |
Reversed Diamond Veneer |
To join veneer you first have to wet strips of veneer tape that are 50mm long, are spaced out across the join. Once you have done this, then you place a strip all the way down the join.
After the lesson today I decided that I would veneer the back of the cupboard. To do this I first went and picked the veneer which I required from the veneer shed.
Next I cut the veneer up to size using a veneer cutter. To do this I worked with others to make it easier.
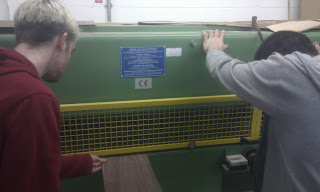 |
Veneer Cutter |
Next I glued the over sized veneer sheets on either side of the backboard, and then placed it into the veneer press for ten minutes. Finally I then cut the over sized veneer to the board size, and then cut the board down to size to create the finished backboard.
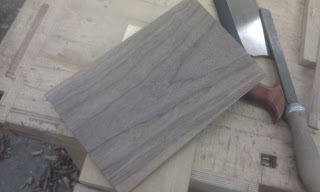 |
Finished veneered backboard |
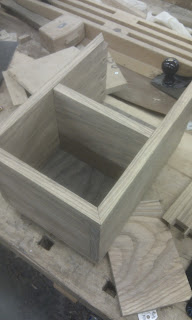 |
Test fitting the backboard in cabinet |